Research Interests
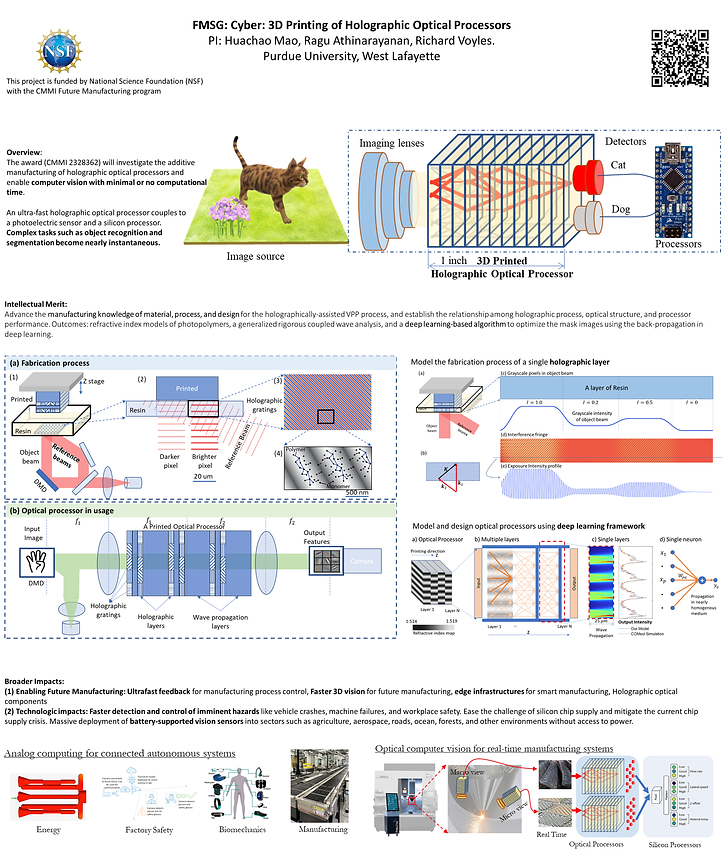
Research I: All printed Optics
1. 3D printing of optical lenses
2. 3D printing of optical computing devices
3. 3D printing of diffractive optical elements
​​
Research II: All printed Microfluidics for Bio-applications
1. 3D printing of volumetric microfluidics, and organs on a chip
2. 3D printing of scaffold for cell studies
3. 3D printing of point-of-care devices
​
Research III: Digital composites
1. Novel multi-material additive manufacturing processes with extensive materials ( viscous polymer-derived resin, fiber-reinforced filaments)
2. Simulation-based and bio-inspired design of composite structures
3. Application of functional composite structures, including
functionally gradient material (gradient stiffness), 4D-material (e.g. temperature-response, magentic-response), 3D electronics, digital composite
​​
Research IV: Scalable micro/nano structures/surfaces
1. Novel additive manufacturing processes with scalable manufacturing capabilities:
surface quality, fabrication speed, ultra-high resolution over large printing volume
2. Design methodologies and tools for multiscale structures
bio-inspired (e.g. shark skin), generative design (lattice cell-based), hybrid design (textures on objects)
3. Applications of multiscale structures, including
ultra-smooth surfaces (e.g. freeform optics), large area textured surfaces (e.g. bio-mimic ), hierarchical structures(e.g. light-weight, strong), lattice/porous structures (light-weight, strong, bio-medical), 3D micro-fluidics
External Grants
-
PI, Manufacturing of High-Performance Tactile Sensors by High Resolution 3D Printing and Conformal Polymer Coating, National Science Foundation, 11/2023 ~ 10/2026, $510,542
-
PI, FMSG: Cyber: 3D Printing of Holographic Optical Processors, National Science Foundation, 01/2024 ~ 12/2025, $497,765
-
Co-PI, Developing Matching Layers through Additive Manufacturing and Conformal CVD Polymer Coating, Baker Hughes Oilfield Operations, Inc, 05/2023 ~ 04/2024, $225,000
-
Co-PI, Improving Energy Productivity and Sustainability of Foundry Metal Casting Lifecycle Operations Using Smart Manufacturing Technologies, DOE / CESMII, 06/2023 ~ 05/2024, $125,000
-
Co-PI, Robotics & Smart Manufacturing, Gene Haas Foundation, 06/2022 ~ 05/2024, $50,000
-
Co-PI, MRI: Development of a Next-Generation 3-D Printer for Smart Product Design - Purdue PolymerMakers, National Science Foundation, 2017 ~ 2023, $ 1,883,017
-
Co-PI, Engineer of the future: preparing the next generation smart/ intelligent manufacturing workforce, DOE / CESMII, 07/2022 ~ 06/2023, $320,000.
​
Internal Grants
-
PI, Optical neural networks for low-power and low-latency computer vision system in autonomous vehicles, Purdue University, $49,978
-
PI, Highly Sensitive Robotic Touch/Pressure Sensors through Sub-10 µm Resolution Additive Manufacturing and Gas-phase Polymer Coating, Purdue University, $15,948
-
Co-PI, Applications-Specific Computer Vision and Real-Time Control, Purdue University, $50,000
-
Co-PI, Highly Sensitive Robotic Touch/Pressure Sensors through Sub-10μm Resolution Additive Manufacturing and Gas-phase Polymer Coating, Purdue University, $15,948
-
Co-PI, Mold-free Highly Sensitive Flexible Pressure Sensors Facile Manufactured by High Resolution 3D Printing and Conformal Polymer Coating Technique, Purdue University, $7,800
-
Co-PI, Immersive Learning Environment for Smart and Connected Supply Chain Operations, Purdue University, $100K.
-
Co-PI, Flexible, Breathable and Customized Health Monitoring Sensors as Human-Machine Interface for Rehabilitation Applications, Purdue University, $2,909
-
Co-PI, : Fourier-Transform Infrared (FTIR) Spectroscopy for Multidisciplinary Research Collaborations for Next Generation Flexible and Wearable Devices and BioSensors. Purdue University, $8,000
​
Projects
Digital Composite
Multiscale Structures (Design, Fabrication, and Applications)
Design of multi-material structures

Eeffective models for multi-material parts are still lacking. The voxelbased multi-material model used in my previous research is memory expensive and hard to design and manipulate. Designer-friendly multi-material model representations and design tools are an urgent demand. Preliminary research has been done to model functionally gradient material with discrete material property.
​
Recent multi-material additive manufacturing (AM) technologies enable the fabrication of parts with different materials. It is now possible to optimize the mechanical properties of parts to meet user requirements using different material compositions, in addition to geometric shapes. Based on simulated data, predicted the material composition for the arbitrary material property.
Multi-material stereolithography (SLA) process
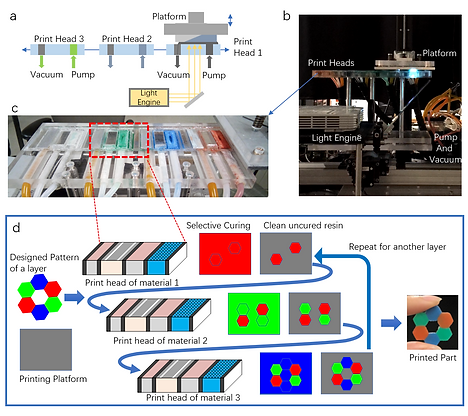
Conventional multi-nozzle ink jetting can only jet out non-viscous photo-curable resin. Syringe-based extrusion method can handle very viscous material, but it is too slow for broader applications. In this work, I propose a new multi-material SLA that can efficiently and effectively handle viscous photo-curable resin. This method utilizes a projector to selectively cure fed liquid resin and then clean the residual uncured resin by a vacuuming device, and then swap to a second resin. By repeating this procedure layer by layer, a 3D model with multiple dissimilar materials can be fabricated.
​
This work of multi-material structures paves the way to 3D printed circuits, functionally gradient material, 4D material, conformal 3D printing and other areas that require functional composites.
Multi-directional conformal additive manufacturing process

Multi-material structures are fabricated by multi-axis conformal 3D printing. By attaching an encapsulated laser on a 5-axis stage and immersing the laser in liquid resin with existing objects, this process draws conformal features on objects’ surface. It can largely reduce support structures and enhance the surface finish and mechanical strength, which is appropriate for the fabrication of 3D curves and shells without staircase defects.
Applications of multi-material structures
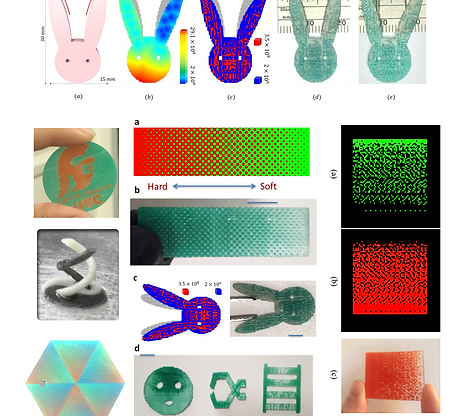
Part of this work received the Outstanding Paper Award in NAMRC conference, and the extended paper was published on Journal of Manufacturing Process. This work of multi-material structures paves the way to 3D printed circuits, functionally gradient material, 4D material, conformal 3D printing and other areas that require functional composites.
Process Planning for Composite Structures
Curved layer deposition

Conventional slicing algorithms for additive manufacturing (AM) processes slice the designed model into a set of planar layers, due to the simplicity, robustness, and generality of most geometries. However, such planar-layer-based slicing significantly limits the performance of the AM system with stair-stepping surface finishing, massive supporting structures, non-conformable to curved substrates, and reduced strength for thin shell structures. To mitigate these drawbacks of planar layer slicing, we presented a curved layer slicing method by utilizing the isothermal surfaces in heat transfer simulation. The designed part is virtually placed on a heated substrate, and the heat spread out through the part, which establishes a temperature field. The isothermal surfaces of this temperature field naturally create curved layers for the printing process. Our method successfully generated curved layers and tool paths for additive manufacturing processes with three-axis and multi-axis 3D printing.
Minimizing printing time and volumetric error

Staircase defects in additive manufacturing significantly reduce the surface roughness, dimensional accuracy, and fatigue strength of printed parts. Adaptive layer thicknesses are promising to reduce the printing time and staircase defects simultaneously. However, conventional adaptive slicing algorithms aim to minimize the number of layers, instead of the actual printing time, and are computationally expensive to evaluate all possible slicing combinations and find the optimal ones. This paper presents a GPU-accelerated slicing algorithm to minimize both the printing time and the volumetric error explicitly and find all the optimal solutions among all possible combinations of layer thicknesses.
Design and fabrication of multiscale structures
Current design tools have difficulty in modeling the multiscale structures, such as hierarchical micro lattices, 3D surfaces with a bundle of microfeatures, hierarchical porous structures and so on. Efficient model representation methods, e.g., LDNI, are exploited. To reproduce mesoscale objects with microstructure in biomimetic products, it is usually difficult to fabricate directly with traditional manufacturing processes such as milling or injection molding. Additive manufacturing (AM), in contrast, is a novel manufacturing technology that fabricates through layer-based directional accumulation with digital information of each layer, regardless of the geometrical complexity of the part. Thus, AM technology is increasingly used in exploring biomimetic applications for its fast prototyping and freedom of geometric design.

Multiscale additive manufacturing process
Conventional AM has difficulty in efficiently fabricating large-scale objects with micro-scale features. To solve the tradeoff among the part size, the feature size and the fabrication speed, I proposed two multiscale AM processes. AM process continuously moved a projector with a 1K resolution to fill the 20K image pattern, that can achieve ultra-high resolution over a very large printing volume.
​
This work advances the AM into areas that need ultra-high resolution over very large printing volume, such as optics, bioinspired functional material, microfluid, biomedical implants, porous membranes, tissue engineering, and energy storage, and so forth

Adaptive slicing: optimize additive manufacturing processes
To further improve the throughput of AM processes,​ I presented a toolpath planning method with scalable layer thickness. The layer thickness was not uniform but adaptive to the geometry error introduced by layered stair-case defects. I formulated the problem as minimizing the total fabrication time given the required surface quality. Moreover, I devised a Dynamic Programming-based algorithm to solve this minimization problem and utilized a GPU technique to boost the algorithm 60 times faster.

Multiscale bioinspired interfacial material
Interfacial material plays a vital role in nature, such as superhydrophobic (lotus leaf), super lubricant (shark skin), fog collection (cactus spikes), super adhesive (gecko feet), self-clean, anti-bioadhesion, anti-icing, anti-fog, anti-fouling, etc. These functions mainly result from the microfeatures array on a large free-form surface. Conventional AM can fabricate these interfacial materials only at millimeter size, which imposes a great limitation for further research and application of the material property at decimeter size. The developed multiscale AM process is one of the enabling technologies that can mimic these nature’s structures at an ultra-high resolution over a large printing volume. The large area 3D interfacial material would find the potential applications in marine engineering, aerospace material, energy harvest, artificial skin, water purification, etc
